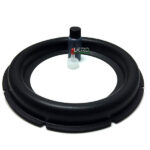
How Do Speakers Get Blown? Why Do They Sound Distorted?
July 13, 2025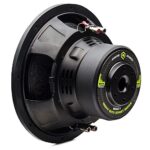
Differences Between SVC and DVC Subwoofers
July 13, 2025Temperature Differences Between Subwoofer Voice Coil Types
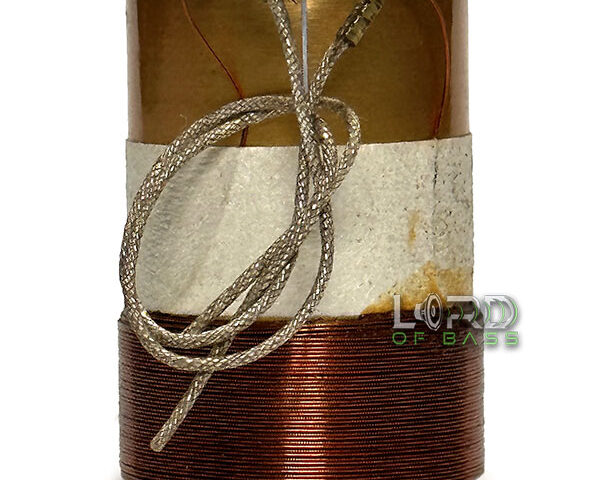
Question: What’s the temperature difference—and the benefits—between aluminum voice coils and Kapton™ voice coils?
Voice Coil Former Types
In subwoofers, the voice coil former (the cylinder around which the voice coil wire is wound) is typically made of one of two materials:
-
Kapton™ (a high-temperature polyimide film)
-
Aluminum
The voice coil’s job is to convert electrical energy into mechanical motion, producing sound. However, much of the electrical energy turns into heat. If this heat isn’t dissipated effectively, it can damage the voice coil.
When a subwoofer’s voice coil heats up, two major issues can occur:
-
Adhesive Failure
The coil’s heat can approach or exceed the melting point of the adhesive holding the coil windings, leading to coil separation and failure. -
Increased DC Resistance (Power Compression)
As the coil heats up, its resistance rises. This reduces the power flowing through it and lowers the subwoofer’s output (Sound Pressure Level, or SPL). This phenomenon is known as power compression.
Kapton™ vs. Aluminum
So, which material is better for a subwoofer voice coil former?
Aluminum Formers
-
Excellent thermal conductivity
-
Helps dissipate heat quickly, reducing the risk of thermal failure
-
Ideal for high-power applications
-
Adds some weight, which can slightly affect moving mass and responsiveness
Kapton™ Formers
-
Very heat-resistant but doesn’t conduct heat as well as aluminum
-
Lightweight, allowing faster cone movement and improved efficiency
-
Less effective at dissipating heat, which could increase power compression during prolonged high-power use
Many wonder:
“If amplifiers use aluminum heat sinks, why would I want plastic (Kapton™) in my woofer’s voice coil former?”
It’s a fair question. Aluminum’s superior heat dissipation makes it an excellent choice for high-power subwoofers where managing heat is critical. However, Kapton™ remains popular for its lightweight properties and high thermal tolerance, making it suitable for certain designs where minimizing moving mass is more important than maximum heat transfer.